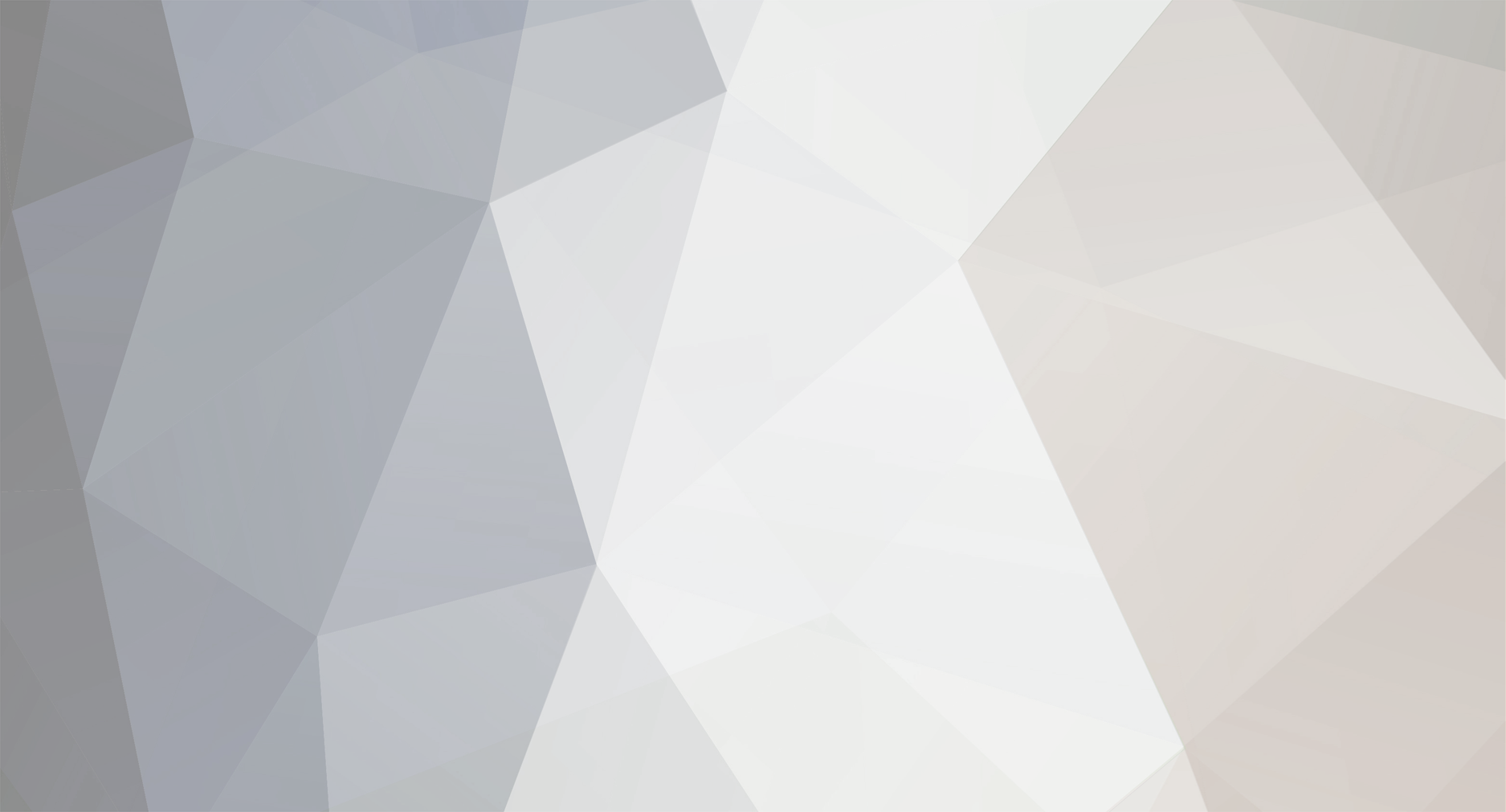
WrineX
Members-
Posts
139 -
Joined
-
Last visited
-
Days Won
1
About WrineX
- Birthday 07/10/1982
Contact Methods
-
Website URL
www.wrinex.com
Profile Information
-
Location
Netherlands
-
Interests
CNC , Diy Audio, Loudspeakers, Planar magnetics, Ribbons.
-
About
Hi my name is Joppe, worked as sound designer and got a passion for designing all sorts of audio related stuff.
-
Interested in Sound for Picture
Yes
Recent Profile Visitors
The recent visitors block is disabled and is not being shown to other users.
-
Hi there, it has been a while ! hope you guys do well? I had this question been ask multiple times now when implementing my chargers into a charge case.. CAN I GET RID OF ALL THOSE POWER BRICKS!!! and well the answer is yes for me ! my chargers can hande around 12-30 volt witch makes it more easy to mate with other chargers powered by one power supply , as well as it can use 24 volt and halve the current requirements for cables and or plugs..... BUT one has many more chargers in the case and they are often not able to do so. So i wondered... maybe i could make a product that can convert from 24Volt to a few set voltages , so we can use a big power brick or somthing else instead of multiple bricks. now my question is , what do you have in your charging cases ? (i am not been on a set for years so). name and number please so i can lookup there requirements. i noticed many have a AA charger thats are fed 5 volt, some have things running on 12 volt.. and my chargers run from 12-30 volt. i would love to know what voltages used mostly and how much they draw, and or how many are used.. so a list of what you have in your charge case would be nice and i do the rest I hope you can help me out ! Kind regards Joppe Peelen
-
Well i got my first charger ready for testing. I changed up the looks this time since i want to be able to make the NP50 and BX1 versions with the same footprint and some of the components. (so i dont have to keep materials for 3 chargers on stock) needs some charge cycles and loading unloading tests it charges 8 batteries at once all at 400mAh so a 1000mAH batteries should be done in around 3 hours +-
-
Well many shipped by now but i thought i make a post anyway. since i forgot. Picture is of Scott Farr's charging case. i dont have the fancy product photos i made with the Np50 yet. Technical specification Charges 8 BX1's Simultaneous. Over sized Converter that can supply up to 2.5 times the current required, to run cool and increase reliability. Matched Charging chips within 1% accuracy. (all pcb's are tested manually). 4.16-4.24 volt with a bias towards the lower end to achieve longer battery life. Swiss made gold plated spring loaded battery contacts. External power supply from a well known brand (Meanwell) Passive cooling. Ability to be fed by a DC power source between 12-48 volts DC (Cart battery or your Car, or a laptop brick) Power supply specifications Power 25 Watt Input range: 85~264 Vac Certificating: CE Cooling : Passive Protection : Short circuit Overload. Over voltage Charger specification Charge rate each slot simultaneous : ~500mA Charge end voltage accuracy: Within 1 % accuracy (all manually tested, and chips replaced if they did not meet this 1% criteria) Protection : Overheat Protection: Charger will cycle down charge current if module reaches above 65+- degrees Celsius. Reverse Polarity Protection Output over/under voltage Over current protection Short circuit protection Thermal shutdown protection Soft start Size : (HxWxL) 4.92 x 11.4 x 6.4 cm. Weight ~500 gram more info and manual can be found here : https://wrinex.com/product/wx-bx1-8/ or you could ask me of course
-
Wrinex Np-BX1 8 Bay Charger First Prototype
WrineX replied to WrineX's topic in Manufacturers & Dealers
Small update, i send out 2 BX1 chargers one has been used allot and works fine, the second has not been used much yet. so i hope to get some info about how it works out. The small fingers that clamp the battery (different then my NP50 chargers) are still being made by hand, not ideal and takes just a bit more fidling around. i hope i can think of a nicer way of bending those fingers. besides that they work. Will be making a dozen soon !- 1 reply
-
- 1
-
-
Thank you sir glad you like them !
-
i know this is an old post, but i stumbled oppon.. but what molds the plastic parts ?
-
Hi there i hope all is fine ? First prototype of the 8 bay NP-BX1 used by Sound Devices in there A20 Mini. It still needs testing ! But at least we are closing in. This is how it looks. if you would like to place an pre order/be on my list or want to know more please mail me @ info@wrinex.com
-
WrineX NP50 Chargers exists officially 1 year, lets celebrate!
WrineX replied to WrineX's topic in Manufacturers & Dealers
That sounds good ! 125 shooting days sounds good to ! -
Hi there since my tiny company exists 1 year i thought its a good time to celebrate that with you guys that made it all possible !!! lets post it here first! Since material prices went up a lot, i had to increase the selling prices a month ago by 25 euro , but i made sure for the celebration you still have a small discount even compared with the old prices. The NP 508 8 bay charger will sell with a 10% discount and will set you back 337.50 euro Ex VAT ex shipping compared to the current price of 375 Euro + a free pig tale to be used on a cart battery. The NP 5016 16 bay charger will sell for 607.50 ex VAT ex shipping compared to 675 + a free pig tale to be used on a cart battery. For more info about the chargers you can check out www.wrinex.com or contact me by mail facebook or the message system over here. A charger can be ordered by mail info@wrinex.com or check out my website. Thank you all for your interest and support, over the year ! it was a great one !!!
-
Np50 Bulk Charger V3.0 Travel edition (on request 16 Bay UPDATE)
WrineX replied to WrineX's topic in Manufacturers & Dealers
Been a while, due to vacation and having to clear a house out. not much had happened from my end as well in terms of orders. but i do not take vacation so if someone still is interested in a charger feel free to contact me here or on wrinex.com have a good one and enjoy the weather, i know i do -
Np50 Bulk Charger V3.0 Travel edition (on request 16 Bay UPDATE)
WrineX replied to WrineX's topic in Manufacturers & Dealers
Since the waiting list is almost gone, i had some time to make a request for a 16 bay version (several people asked for one, but i could not make one since there where so many pre orders). i still recommend 2 x 8 bay because of redundancy , but if you got many to charge, or want to have as small of a kit possible. this is it. 16 bays charging in one go. same specs as the smaller 8 bay in terms of speed. it does use a slightly more powerful power brick of course. that can also be used on the smaller one if needed. Both can be used on a cart battery as well if it is able to supply 20 watts for the 8 bay and 40 watts for the 16 bay charger. DC voltage range for the 16 bay = 12-24volt 40 watts Price is 650 Euro ex VAT ex shipping compared to 350 for the 8 bay. both can be ordered by contacting me More specs about the 8 bay can be found on www.wrinex.com (webshop part not yet up) -
Np50 Bulk Charger V3.0 Travel edition (on request 16 Bay UPDATE)
WrineX replied to WrineX's topic in Manufacturers & Dealers
It has been quite the year !! And i have to thank you all for putting trust in me and my product. And i hope everyone that owns one enjoy using them (sorry about the disco in every hotel room) For the people that are still on the waiting list, my list is almost gone and i bought allot of stock for parts, so i should be able to deliver faster. i send everyone an email to wish you all happy holidays, but some might not be in my current list. So thank you once more to make this possible and enjoy the holidays! Kind regards Joppe Peelen -
Np50 Bulk Charger V3.0 Travel edition (on request 16 Bay UPDATE)
WrineX replied to WrineX's topic in Manufacturers & Dealers
haha it is dwarfed by your huge case haha -
Np50 Bulk Charger V3.0 Travel edition (on request 16 Bay UPDATE)
WrineX replied to WrineX's topic in Manufacturers & Dealers
Nice one thank you for the picture ! Also nice USB leads, for timecode devices ? i hope you will enjoy the charger, if you got any questions feel free to ask. Kind regards Joppe Peelen